Professional bike teams spend millions on optimizing their material. They try hard to make the bikes lighter. They turn every piece of the bike upside down to find out, where there is weight to be saved. To evaluate, if an idea for a solution is valuable, 3D-printing is a fast method to turn ideas into prototypes. Why shouldn´t every bike manufacturer learn from the pros and use 3D-printing to become more agile in prototyping or for the production of end-use parts. As technical differentiation becomes harder to leverage, design wise differentiation becomes more important. We talked with Gert Hendrickx from Materialise about the value and the affordances of using 3D-printing on a regular basis.

Gert, what's your job at Materialise?
I'm the global sales director in the manufacturing division. Responsible and dealing with all the sales within the manufacturing department. We develop software, we have solutions for the medical industry and we manufacture 3D printed parts
How are the income streams within your area?
For the Materialise Manufacturing segment, our revenue in 2022 was around 103 million Euros. In Materialise manufacturing, we make the distinction between prototyping and certified manufacturing. Prototyping is a one-off part used for testing, product validation, or design verification. And then customers can go for serial production with 3D printing, which is small series. and that's what we call certified manufacturing.
How much metal, how much plastic?
Today, metal is roughly 10% of what we do. We started about 30 years ago here in Leuven with plastics. The whole metal part is supported with the team in Bremen, in our metal competence centre.
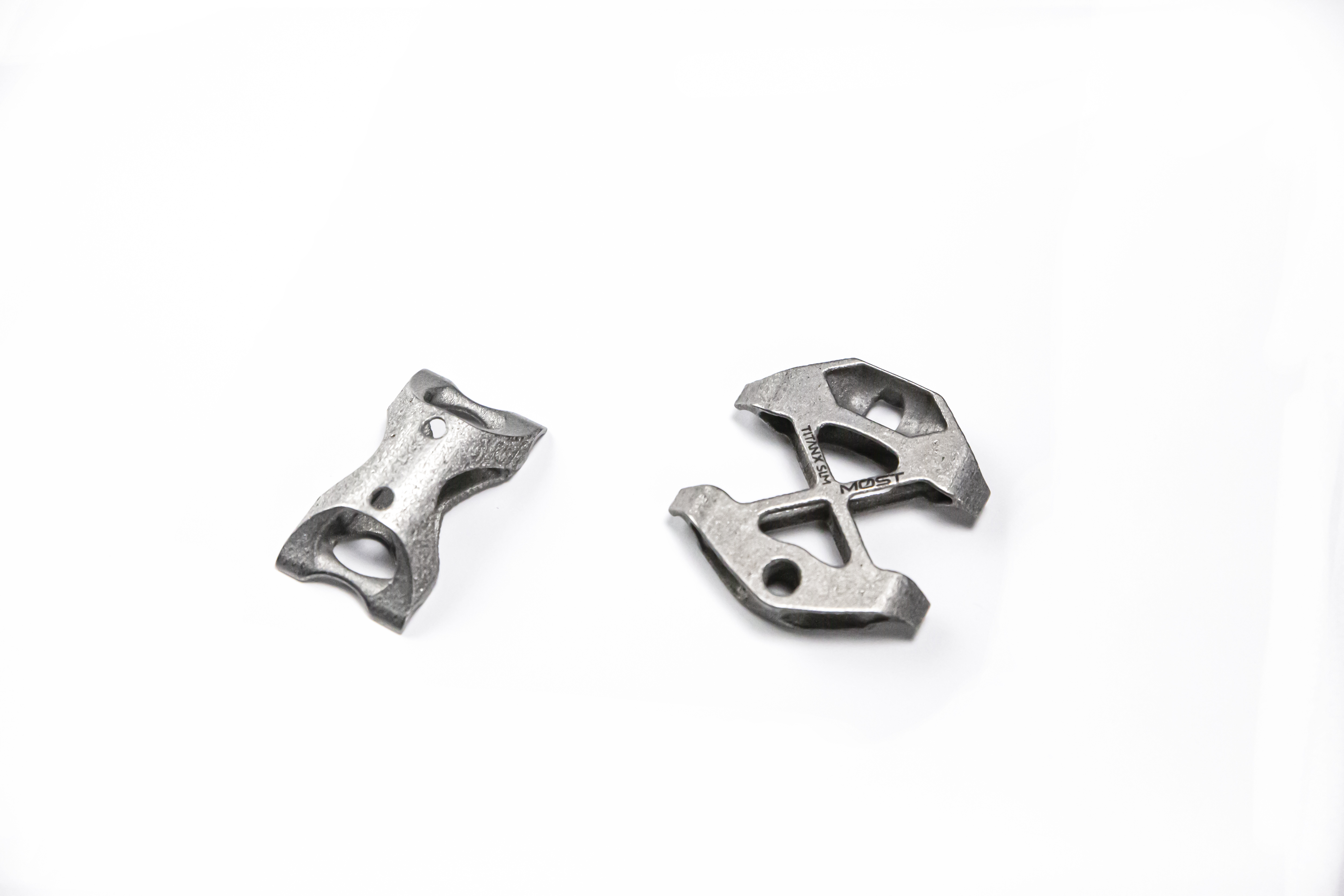
How do you calculate if, or whether it's prototyping only, or whether it goes into smaller series?
This is always based on the needs of the customer, and the part requirements. With prototypes the customer will be looking to produce parts for testing and validation in the product development cycle, usually as a one-off or small quantity. For small series, they will want to use 3D printing to manufacture the final product. With manufacturing using 3D printing the customer will have different requirements in terms of repeatability and reliability, and quality too. I would say sometimes the paperwork or certification requirements that comes with it are different than those for prototying. As an example, we work for Airbus. You can imagine that the amount of paperwork and certifications that we have to provide for the aerospace industry is completely different. It doesn´t make sense to go all through this for one prototype as is not required.
How much of the bike can we print in 3D? Not as prototype, but maybe as sellable.
That's a good question. What we do now is, we are producing both prototypes and series parts. In theory, everything that is plastic and metal, could be printed. What we, as Materialise, work with you on is whether it should be printed – does it make sense from a manufacturing or supply chain point of view. Not every part makes sense to print.
For the time being, it is mainly the frames, in prototyping and we work also on the saddle components. For example we work with Pinarello; we produce the saddle pin to connect the saddle to the tube that goes in the frame.
And it can be printed in the same quality in terms of stability and stuff.
We work hard to ensure that series parts meet strict requirements, in terms of repeatability and reliability. You can run into your limitations, of course, but this is about finding the right parts to use the technology for. You can go very complex and in very intricate shapes. At the end , the parts have to pass the tests such as fatigue test and load testing of course.
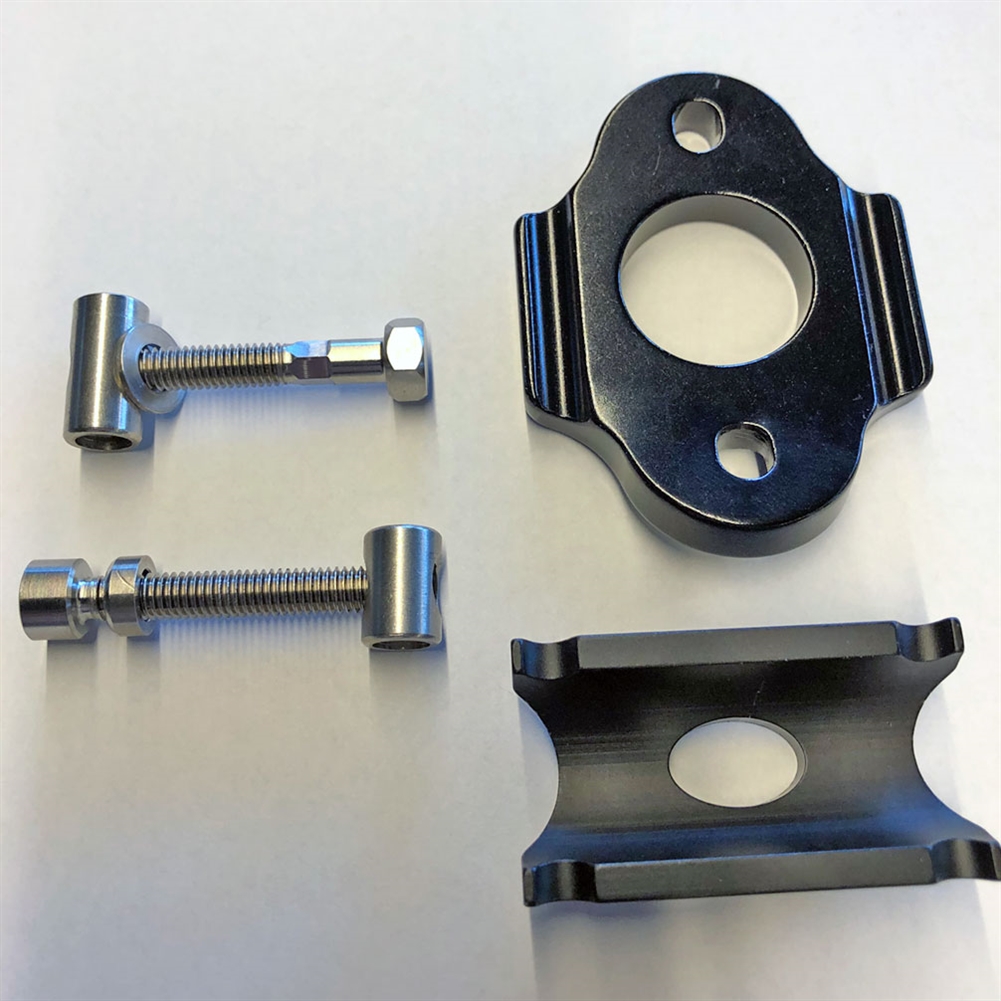
What are the possibilities?
We see an increase in demand in the biking industry. So, we are working now for several bike manufacturers to make the prototypes of their products.
The majority of the parts that we are printing, is indeed for showcases, or to make pictures of a new model. The next step, I think, and that's my personal opinion, can be that you make frames really customized, that we start measuring people.
And also, I want to come back to the number of parts that you need. If it goes to 50,000, 60,000, 100,000 parts, then additive manufacturing is not used anymore, except for cases like Pinarello, where it is still worthwhile to do the additive manufacturing. It all depends on the number and design of the parts.
To go from traditional manufacturing methods to additive manufacturing, it can be price-related or price-driven, or even supply-chain driven. For Pinarello it is really about the weight decrease that drives the use of the technology.
Are processes within the manufacturers ready for this idea of production?
The sooner a company like Materialise is involved in the design process, the better and the more benefit both our customers and ourselves can have. A lot of companies come to Materialise with a set of drawings and ideas. But in fact, that can alreadybe too late because then we have to make adaptions to make it fit the technology. Ideally, we start together with a bold idea like: Let´s bring down weight by 10% as an example.
Where's the critical point? Where is too late?
It's never too late. I mean, the later we bring additive manufacturing in the process, the more I believe we have to do modifications on what the customer already developed. We believe in a more agile way of development, following the 3E-principle: explore, experiment and enable. The sooner you are in those three steps, the more benefit you get. Sometimes our modifications even change the project, because the customer would have to go back to the product development, the design team and refine processes there.
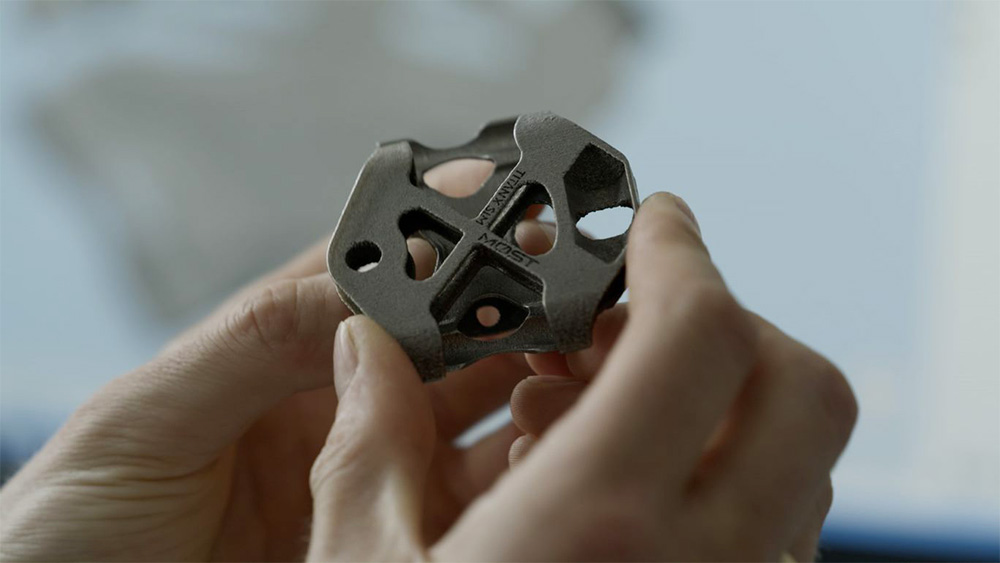
How long is the printing process? 3D printing is said to be slow.
It all depends on the technology you are using, and the parts being produced. We have printers here that are printing for four days, but we also have printers here that are working for two hours. It heavily depends on the size of the product.
Aren't the innovation departments at your customers used to shorter development cycles?
We do not get many complaints there. The expectations of the customer and our deliveries, they are set quite right. With 3D printing we can speed up the development time anyway significantly,because we have fast iterations using digital files. This is a key benefit for using 3D printing.
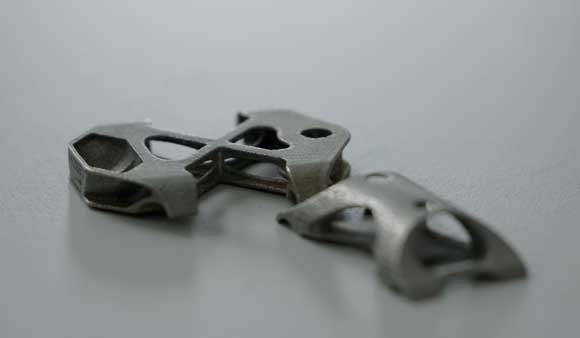
And the detail level or even the size of the 3D-print can vary from stage to stage.
Exactly. In the beginning it might be plastic models, in the end it´s the full-fledged metal print.
Is printing plastic faster, then printing metal?
No.
What will be the essence of your talk at Bike Bize Revolution?
The expression VUCA stands for volatility, uncertainty, complexity, ambiguity in these times. It´s used fairly negative. I would like to rephrase that into something positive. If you have agile methods in place, for whatever area there is, you don´t fear change, you embrace it.
And of course we will bring 3D-printed parts with us, so attendees can touch and feel what is possible with additive manufacturing.
Gert Hendrickx
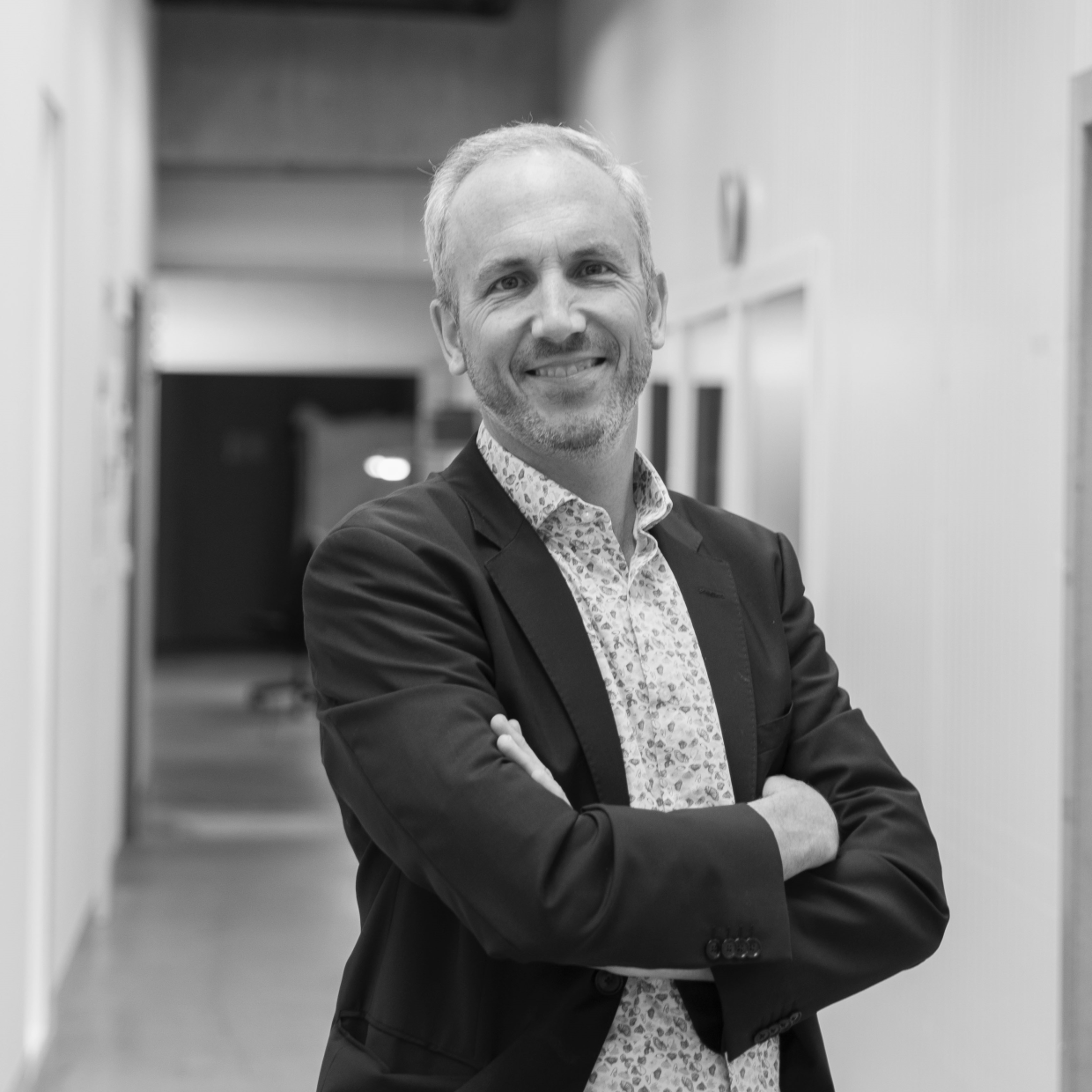
With over 25 years of experience in not only technical & commercial positions but also managerial and leading roles in a variety of companies and countries spread over 5 continents, Gert Hendrickx joined Materialise now 1.5y ago as Global Sales Director.
In this role, Gert is responsible for the global development, implementation and follow up of the sales strategy and growth within the Core Manufacturing BU.
This BU represents over 50 mio EUR turnover per year.
Gert is a Master in Science, graduated from the University of Leuven, will be 50 this year, married with Sophie and proud father of 3 teenage daughters.
During his free time, Gert rides the mountain bike, likes skiing and in the little time that remains, the old-timer BMW comes out for a ride or to fix it before the ride.