Profi-Radteams geben Millionen für die Optimierung ihres Materials aus. Sie versuchen alles, um die Fahrräder leichter zu machen. Sie stellen jedes Teil des Fahrrads auf den Kopf, um herauszufinden, wo sich Gewicht einsparen lässt. Um zu bewerten, ob eine Idee für eine Lösung wertvoll ist, ist der 3D-Druck eine schnelle Methode, um Ideen in Prototypen umzusetzen. Warum sollte nicht jeder Fahrradhersteller von den Profis lernen und den 3D-Druck nutzen, um beim Prototyping oder bei der Produktion von Endverbrauchsteilen flexibler zu werden? Da es immer schwieriger wird, sich technisch zu differenzieren, wird die Differenzierung durch das Design immer wichtiger. Wir sprachen mit Gert Hendrickx von Materialise über den Wert und die Möglichkeiten der regelmäßigen Nutzung des 3D-Drucks.

Gert, was ist Ihre Aufgabe bei Materialise?
Ich bin der globale Verkaufsleiter in der Fertigungsabteilung. Ich bin für den gesamten Vertrieb innerhalb der Fertigungsabteilung verantwortlich. Wir entwickeln Software, Lösungen für die medizinische Industrie und wir stellen 3D-gedruckte Teile her.
Wie sehen die Einkommensströme in Ihrem Bereich aus?
Für den Bereich Materialise Manufacturing lag unser Umsatz im Jahr 2022 bei rund 103 Millionen Euro. Bei Materialise Manufacturing unterscheiden wir zwischen Prototyping und zertifizierter Fertigung. Prototyping ist ein einmaliges Teil, das für Tests, Produktvalidierung oder Designverifizierung verwendet wird. Und dann können die Kunden mit dem 3D-Druck in die Serienproduktion gehen, also in Kleinserien, und das nennen wir zertifizierte Fertigung.
Wie viel Metall, wie viel Kunststoff?
Heute macht Metall etwa 10 % unserer Arbeit aus. Wir haben vor etwa 30 Jahren hier in Leuven mit Kunststoffen angefangen. Der gesamte Metallbereich wird von unserem Team in Bremen, in unserem Metallkompetenzzentrum, betreut.
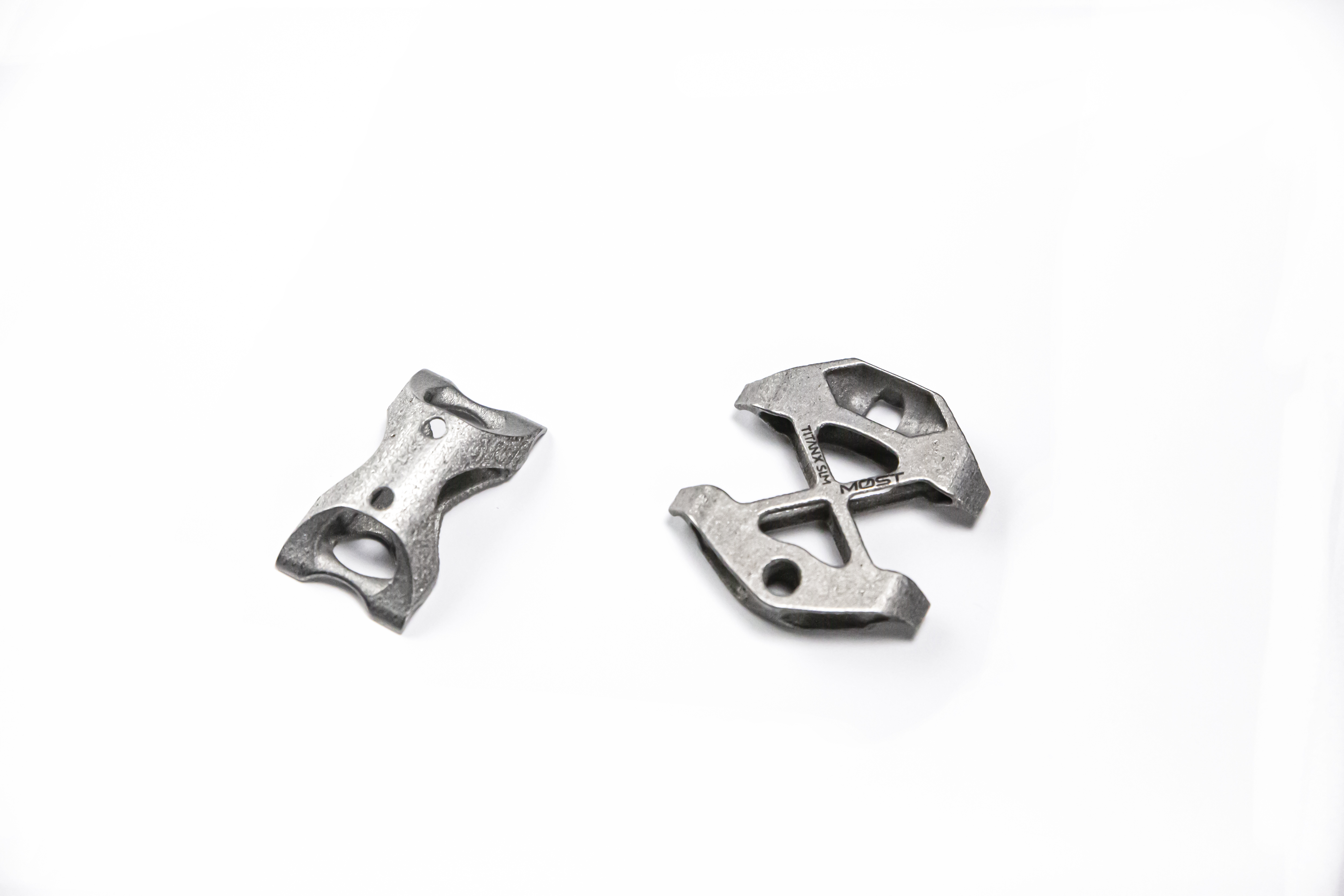
Wie kalkulieren Sie, ob es sich nur um Prototypen handelt oder ob es in kleinere Serien geht?
Das hängt immer von den Bedürfnissen des Kunden und den Anforderungen an das Teil ab. Bei Prototypen geht es dem Kunden um die Herstellung von Teilen für die Prüfung und Validierung im Produktentwicklungszyklus, in der Regel als Einzelstück oder in kleinen Mengen. Bei Kleinserien wird der Kunde den 3D-Druck für die Herstellung des Endprodukts nutzen wollen. Bei der Fertigung im 3D-Druck stellt er andere Anforderungen an die Wiederholbarkeit und Zuverlässigkeit sowie an die Qualität. Ich würde sagen, dass der damit verbundene Papierkram oder die Zertifizierungsanforderungen manchmal anders sind als beim Prototyping. Wir arbeiten zum Beispiel für Airbus. Sie können sich vorstellen, dass die Menge an Papierkram und Zertifizierungen, die wir für die Luft- und Raumfahrtindustrie vorlegen müssen, völlig anders ist. Es macht keinen Sinn, all dies für einen Prototyp zu erledigen, da dies nicht erforderlich ist.
Wie viel des Fahrrads können wir in 3D drucken? Nicht als Prototyp, aber vielleicht als verkaufsfähiges Modell.
Das ist eine gute Frage. Was wir jetzt machen, ist, dass wir sowohl Prototypen als auch Serienteile herstellen. Theoretisch könnte alles, was aus Kunststoff und Metall besteht, gedruckt werden. Wir von Materialise arbeiten mit Ihnen zusammen, um herauszufinden, ob das Teil gedruckt werden sollte - ob es aus Sicht der Herstellung oder der Lieferkette sinnvoll ist. Nicht bei jedem Teil ist es sinnvoll, es zu drucken.
Im Moment sind es vor allem die Rahmen im Prototyping und wir arbeiten auch an den Sattelkomponenten. Wir arbeiten zum Beispiel mit Pinarello zusammen; wir produzieren den Sattelstift, der den Sattel mit dem Rohr im Rahmen verbindet.
Und er kann in der gleichen Qualität gedruckt werden, was die Stabilität und das Material angeht.
Wir arbeiten hart daran, dass die Serienteile strenge Anforderungen erfüllen, was Wiederholbarkeit und Zuverlässigkeit angeht. Natürlich kann man an seine Grenzen stoßen, aber es geht darum, die richtigen Teile für die Technologie zu finden. Sie können sehr komplex und in sehr komplizierten Formen hergestellt werden. Am Ende müssen die Teile natürlich Tests wie Ermüdungstests und Belastungsprüfungen bestehen.
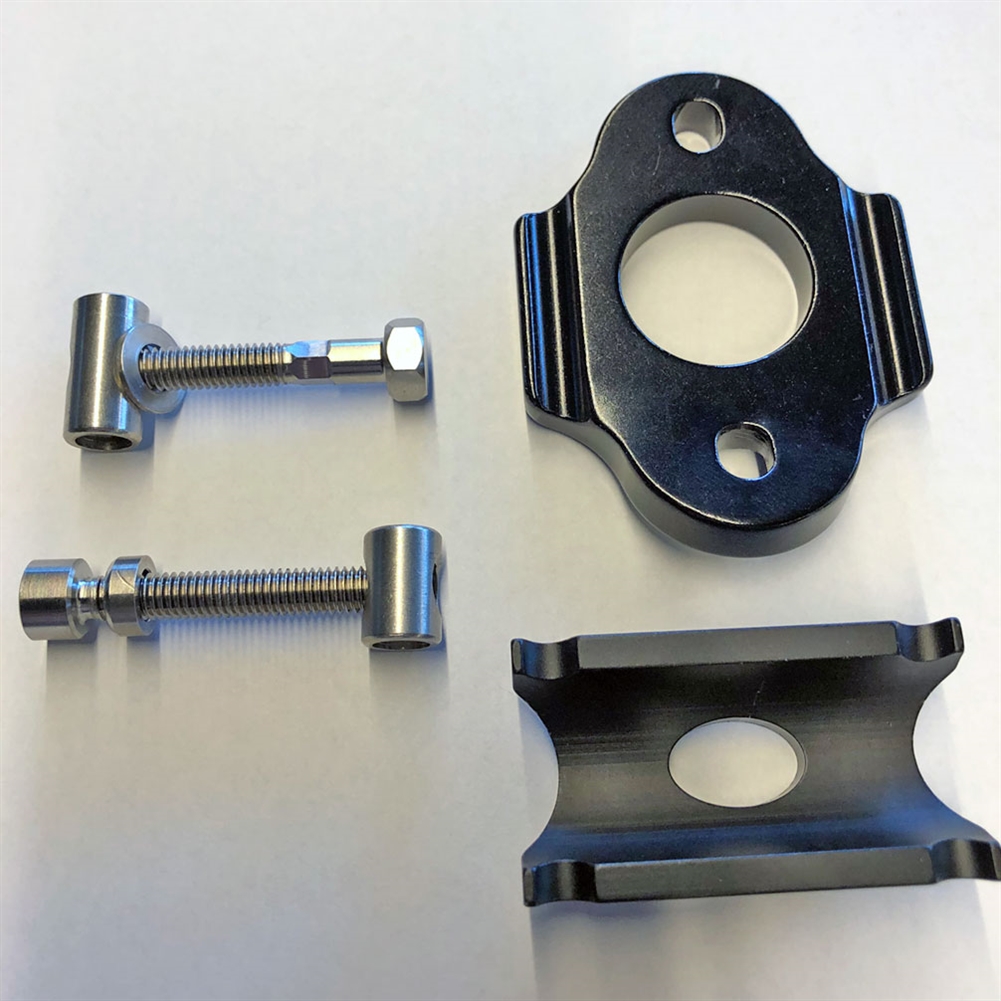
Was sind die Möglichkeiten?
Wir sehen einen Anstieg der Nachfrage in der Fahrradindustrie. Deshalb arbeiten wir jetzt für mehrere Fahrradhersteller, um die Prototypen ihrer Produkte herzustellen.
Die meisten Teile, die wir drucken, sind in der Tat für Vitrinen oder um Bilder von einem neuen Modell zu machen. Der nächste Schritt, und das ist meine persönliche Meinung, kann darin bestehen, dass wir Rahmen nach Maß anfertigen, dass wir anfangen, Menschen zu vermessen.
Und ich möchte noch einmal auf die Anzahl der benötigten Teile zurückkommen. Wenn es um 50.000, 60.000, 100.000 Teile geht, dann wird die additive Fertigung nicht mehr eingesetzt, außer in Fällen wie bei Pinarello, wo es sich immer noch lohnt, die additive Fertigung durchzuführen. Es hängt alles von der Anzahl und dem Design der Teile ab.
Der Wechsel von traditionellen Fertigungsmethoden zur additiven Fertigung kann preisabhängig oder preisgesteuert sein, oder sogar von der Lieferkette abhängen. Für Pinarello ist es vor allem die Gewichtsreduzierung, die den Einsatz der Technologie vorantreibt.
Sind die Prozesse innerhalb der Hersteller bereit für diese Idee der Produktion?
Je früher ein Unternehmen wie Materialise in den Designprozess einbezogen wird, desto besser und desto mehr Nutzen können sowohl unsere Kunden als auch wir selbst daraus ziehen. Viele Unternehmen kommen mit einer Reihe von Zeichnungen und Ideen zu Materialise. Aber eigentlich kann das schon zu spät sein, denn dann müssen wir Anpassungen vornehmen, damit es zur Technologie passt. Im Idealfall beginnen wir gemeinsam mit einer kühnen Idee wie: Lassen Sie uns zum Beispiel das Gewicht um 10 % senken.
Wo ist der kritische Punkt? Wo ist es zu spät?
Es ist nie zu spät. Ich meine, je später wir die additive Fertigung in den Prozess einbringen, desto mehr glaube ich, dass wir Änderungen an dem vornehmen müssen, was der Kunde bereits entwickelt hat. Wir glauben an eine agilere Art der Entwicklung, die dem 3E-Prinzip folgt: explore, experiment and enable. Je früher man diese drei Schritte durchläuft, desto mehr Nutzen hat man. Manchmal verändern unsere Änderungen sogar das Projekt, weil der Kunde zurück zur Produktentwicklung und zum Designteam gehen und dort die Prozesse verfeinern muss.
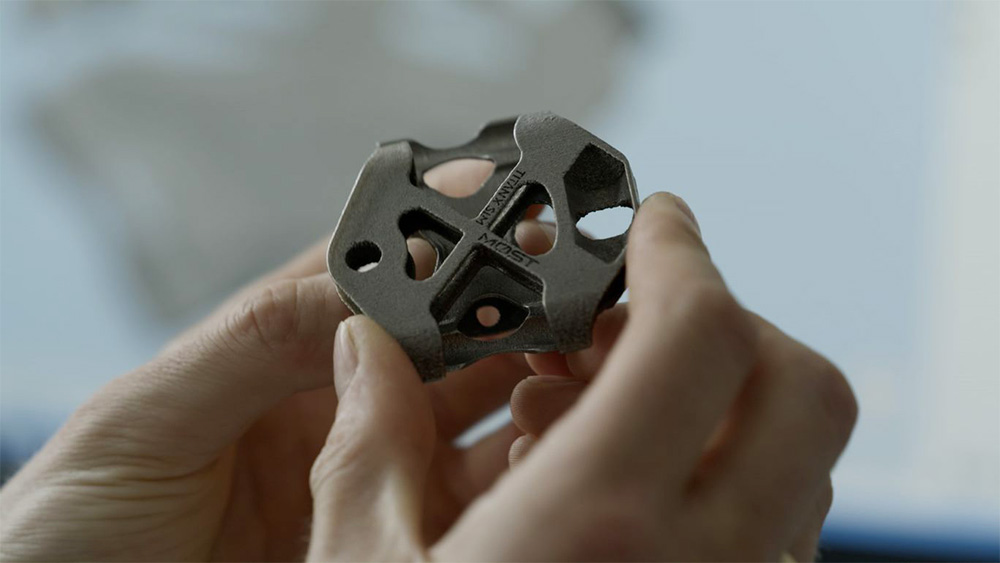
Wie lange dauert der Druckprozess? Es heißt, der 3D-Druck sei langsam.
Das hängt von der verwendeten Technologie und den herzustellenden Teilen ab. Wir haben hier Drucker, die vier Tage lang drucken, aber wir haben auch Drucker, die zwei Stunden lang arbeiten. Es hängt stark von der Größe des Produkts ab.
Sind die Innovationsabteilungen Ihrer Kunden nicht an kürzere Entwicklungszyklen gewöhnt?
Wir bekommen dort nicht viele Beschwerden. Die Erwartungen der Kunden und unsere Lieferungen, die sind ganz richtig eingestellt. Mit dem 3D-Druck können wir die Entwicklungszeit ohnehin erheblich beschleunigen, weil wir schnelle Iterationen mit digitalen Dateien haben. Dies ist ein wesentlicher Vorteil des 3D-Drucks.
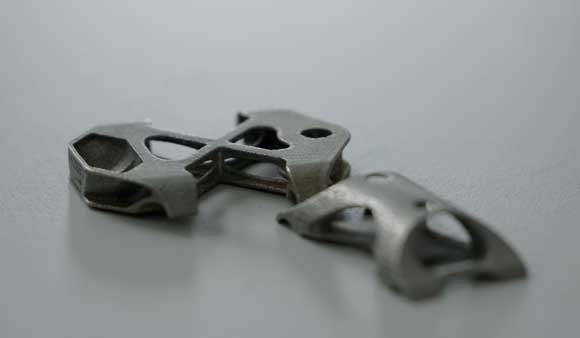
Und der Detailgrad oder sogar die Größe des 3D-Drucks kann von Stufe zu Stufe variieren.
Ganz genau. Am Anfang sind es vielleicht Plastikmodelle, am Ende ist es ein vollwertiger Metalldruck.
Ist das Drucken von Kunststoff schneller als das Drucken von Metall?
Nein.
Was wird die Essenz Ihres Vortrags auf der Bike Bize Revolution sein?
Der Ausdruck VUCA steht in der heutigen Zeit für Volatilität, Unsicherheit, Komplexität, Mehrdeutigkeit (volatility, uncertainty, complexity, ambiguity). Er wird eher negativ verwendet. Ich würde das gerne in etwas Positives umformulieren. Wenn man agile Methoden einsetzt, egal für welchen Bereich, hat man keine Angst vor Veränderungen, sondern nimmt sie an.
Und natürlich werden wir 3D-gedruckte Teile mitbringen, damit die Teilnehmenden anfassen und fühlen können, was mit additiver Fertigung möglich ist.
Gert Hendrickx
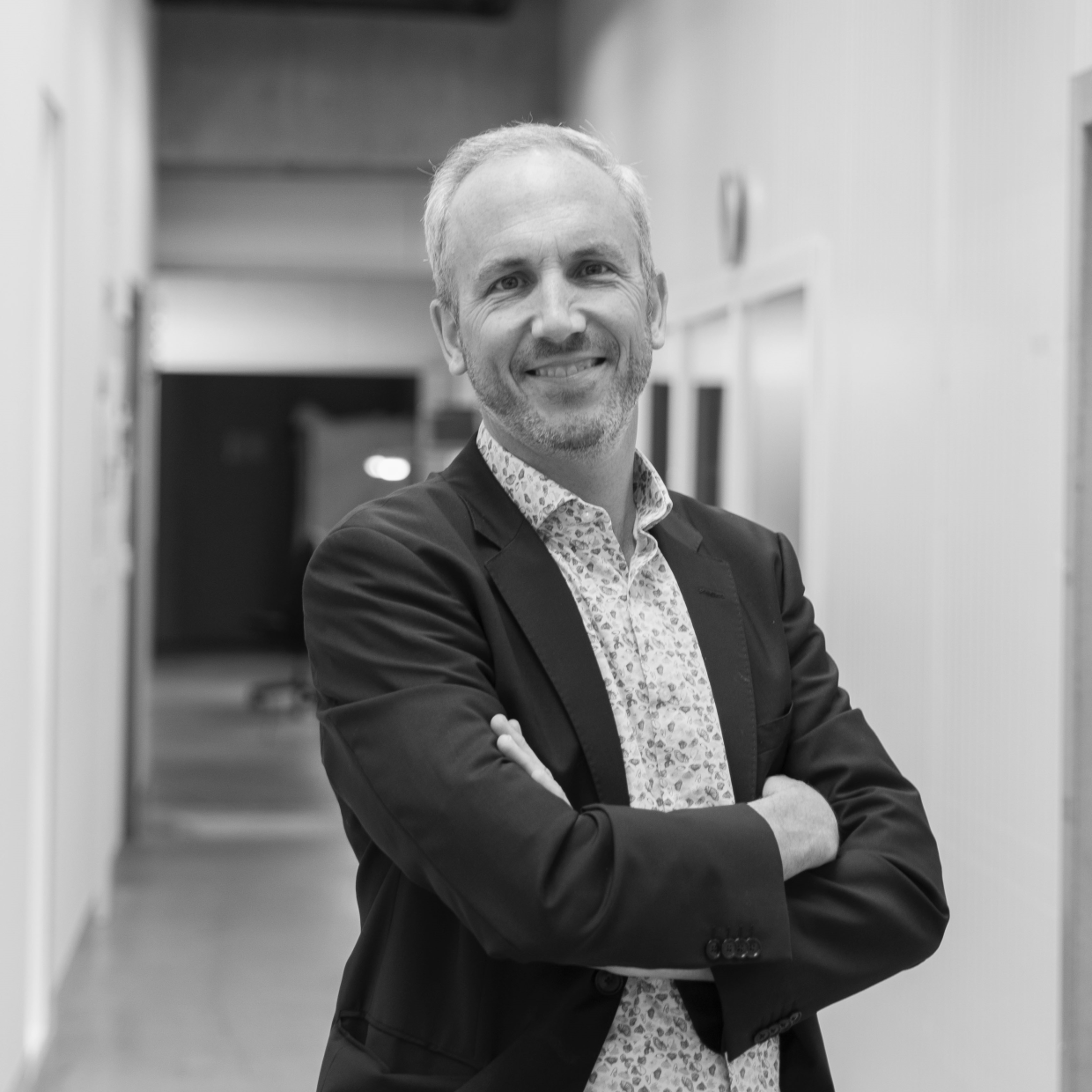
Gert Hendrickx verfügt über mehr als 25 Jahre Erfahrung nicht nur in technischen und kaufmännischen Positionen, sondern auch in Management- und Führungspositionen in einer Vielzahl von Unternehmen und Ländern auf fünf Kontinenten. Vor 1,5 Jahren kam Gert Hendrickx als Global Sales Director zu Materialise.
In dieser Funktion ist Gert Hendrickx für die globale Entwicklung, Umsetzung und Verfolgung der Vertriebsstrategie und des Wachstums innerhalb der Kerngeschäftseinheit Fertigung verantwortlich.
Diese Geschäftseinheit repräsentiert über 50 Mio. EUR Umsatz pro Jahr.
Gert hat seinen Masterabschluss in Naturwissenschaftenan an der Universität von Leuven gemacht,.
Er wird dieses Jahr 50 Jahre alt, ist mit Sophie verheiratet und stolzer Vater von 3 Töchtern im Teenageralter.
In seiner Freizeit fährt Gert Mountainbike, geht gerne Skifahren und in der wenigen Zeit, die ihm bleibt, fährt er seinen BMW-Oldtimer aus oder repariert ihn vor der Fahrt.